A Long Time in the Making
Ever since completing the 6336 SET back in 2017 this amp has been bouncing around in my head. The big SET has a lot going for it, however there is a high price to be paid in both amplifier infrastructure and operational heat. And that price is basically for a handful of dBs (≈4.4dB in the end) difference in peak power performance. I had developed a design for a 6AS7 SET driven by a 12AX7 several years before but was never happy with that design. However, once I developed the high voltage swing driver for the 6336 SET, it opened up all kinds of new possibilities.
Finally in the fall of 2020 I had decided that the time was ripe for the new SET. This was to be an amplifier that sits, in terms of power, right between the small SETs like the 6CY7 Zebrawood amp and the big 6336 SET amp. And after much investigation, I settled on the 6AS7 dual power triode. My calculations showed I should be able to get between two and three clean watts out of each triode and maybe up to four before the distortion got too bad.
Now, with decisions made for both the driver and the power tube, it was time to formalize the design and get going.
The Electrical Design
With the driver stage already throughly investigated for the 6336 SET, the design for this amp turned to the 6AS7 power triode. After investigating several different plate loads I settled on a 2.5kΩ load for each triode. This value presents a good compromise between power and distortion. Since this tube is rich in second harmonic character, I chose what I thought was a balanced bias point between conduction and cutoff. Here is my load line design for the power stage.
This design places the output power into the transformer at about three watts peak. Assuming an 80% transformer efficiency, this equates to about 2.4W peak power out. This was, I decided, a good design solution for the class of SET I wanted. This is not to say that the power output is limited to this, but this is the clean power out design point. It is entirely possible to drive the speakers up to about 4W before the odd order distortion becomes noticeable. This assumption has proven to be correct in initial auditions of the amplifier.
Although I already had the driver stage design, there were a couple of changes I wanted to make for this amp. These are all component changes to support the desired amplifier bandwidth. For reference, here is the final as-built amplifier and power supply schematic.
The changes to the driver were all capacitative changes. The danger in using too large a coupling or bypass capacitor lies in what happens when the grid goes into conduction. But since I had already determined that the driver can go to well over +/-90V peak, I knew that the the power stage would be the first to enter an overdrive condition. This makes only the second coupling cap in any way critical.
So for the driver for this amp, I increased the first stage bypass to 47µf and the first coupling capacitor to 0.068µf. I felt comfortable with a 68µf power stage bypass value as well. I had reason to believe that the power stage cathode impedance I calculated from the load line design was actually lower than calculated based on some prototyping work. This left only the last coupling capacitor. After running the calculations I decided to increase this capacitor to 0.1µf. This places the -3dB rolloff point at ≈2.8Hz with a recovery time constant of ≈56ms. This is normally a little longer than I’d like but the risk of blocking at over full power is relatively low.
With these decisions made and incorporated into the final schematic the, electrical design was complete.
The Build
The build for this amplifier followed a long and twisted road. It started with trying to choose wood from several different hardwood species. These are the five finalists:
There are from left to right, Bloodwood (fine grain), Bloodwood (coarse grain), Purpleheart, Wenge, Bubinga, and Padauk. At the time I also had the idea that I should be using copper for the top and front plates. Having settled on the purpleheart, I began to give consideration to the copper. I finally decided that I was going to use an oil finish on the wood and use a tarnish patina on the copper. This decision led to a long series of investigations and experiments attempting to find the way to achieve the copper patina I wanted.
I also hadn’t decided on the top layout at this point. I kept going back and forth between symmetric and asymmetric designs. I finally decided on a nice symmetric design with rectifier and power tube on the midline of the amp. Here’s the top layout. This top plate is 12″ (≈305mm) wide and 10″ (≈254mm) deep.
This layout gives ample separation for air flow on top and and ease of wiring beneath. I have a dimensioned diagram if anyone would like one.
The final decisions for the overall look and feel of the amplifier took considerably longer than any other decisions up to this point. After several months of twists, turns, and dead ends, I finally arrived at the look I wanted for the new amp. And it took me until March of this year to finally get it right. Here is the finished purpleheart chassis with the patina colored copper in place.
The picture really doesn’t do justice to the copper finish. It is beautifully aged just like it’s been in use for decades. With all the subtile variations one would expect from something that’s been around for quite a while.
Once to this point assembly proceeded rather quickly. Here are the ring frame chassis with all the attached wiring, and the underside of the top plate with all the wiring and components in place.
Once things had progressed to this point it was a simple matter to marry the top plate to the ring frame and connect up the remaining wiring. Here’s how it looked with everything except the final power supply dropping resistor in place.
The final step at this point is, after a final wiring check and an AC operation check without tubes, to install the tubes, apply power, and dial-in the B+ voltage. Here is the amp, sitting in a cradle, with a high power variable resistor temporarily wired into the power supply.
I dialed in the B+ voltage for the power stage. This required a 200Ω resistance to get the power stage voltages down to ≈267v. With this load for the power stages, the driver B+ voltages were 306v. This is a good operating spot for the cascaded drivers providing lots of clean swing to drive the plower triodes.
I didn’t have an appropriate 200Ω dropping resistor so I did what any good Engineer would do. I improvised. I did have in my stock a pair of 400Ω 1% wire-wound power resistors so I used them in parallel. Here they are installed in the amplifier.
The final act of assembly was to take a set of voltage readings in the final configuration to make sure everything is per design. Here are the measured bias voltages and operating conditions prior to installing the bottom plate on the amp.
The power stage bias voltages are a little above the design point, but not enough to worry about. And the plate dissipations on the big triode are well within acceptable limits. The bias conditions on the drivers are also very close to the design points. At this point I closed up the amp and got ready to test.
And here’s how it looks from the back showing the audio inputs and outputs and the power connection and fuse.
Initial Listening and Break-in
So I didn’t progress directly to testing. It was late in the afternoon when I finished so I plugged in the amp and let it fly. I was not disappointed! Over the course of about six hours I threw every type of music imaginable at this amp and it handled all of it flawlessly. From the very fast, to the slow, to deep bass, to crisp high frequencies, even harmonically difficult choral music and Gregorian chant sounded amazing. It was by far the best break-in session I have ever had with an amplifier.
Testing
The first step in testing was to determine the power and distortion characteristics for the amp. Here are the numbers for the first tube.
This data was with a JAN 6080 power tube in the amp. I chose this tube because I didn’t want to risk any of my older ST shaped 6AS7Gs until I was sure of the amp. The left channel distortion numbers were much higher than the right channel and the gain was noticeably lower. After swapping a couple of tubes, the left channel distortion numbers better aligned with the right channel and I moved forward.
I did not detect this difference auditorily during the initial listening and break-in. However I wanted better matched channels as I continued. One of the things I commented on in a post a while back was the variability of the examples of 6080s and 6AS7s I’ve seen. Using this tube it is probably a very good idea to try out several tubes to find the ones you like. I also may try a few new stock Svetlana 6AS7s to see if they are more uniform than the older tubes.
The peak numbers for power here are based on looking at waveforms on the oscilloscope and trying to detect asymmetries. However, I drove the amplifier to over 3.5W to get to the traditional 5% distortion number. But the distortion waveform had more odd harmonics than I generally prefer. Regardless, the amp sounds really good putting out between two and three watts.
The next step was the bandwidth check. When I started I was very hopeful because I had made several changes specifically to support a good amplifier bandwidth. As it turns out there was no reason for concern. The bandwidth of the amp is excellent. Here is the plot of end-to-end relative gain and phase for the amplifier.
Due in no small part to the low Rp of the power triode and the changes I made to support the low end this amp goes down to 20Hz with essentially no falloff in performance. The response is down -0.11dB at 20Hz, -0.72dB at 15Hz, and -3.5dB at 10Hz. This is exceptionally good low end performance for a capacitively coupled vacuum tube amplifier. At the high end the amp is only down -1.31dB at 20 kHz. There is a gentle rolloff of about a 1.1dB between 1kHz and 18kHz due to the Miller capacitance of the power triode in combination with the exceptionally high output impedance of the unbypassed second driver stage. This was expected and as it’s only a dB, it is imperceptible in use. So the 1dB bandwidth of the amplifier is approximately 15Hz to 18kHz. This is GREAT performance.
Given the very good low end performance in the bandwidth, I decided to perform a low end distortion check as well. Many times, especially with beam power tubes in an SE-UL topology, the distortion at low frequencies can become rather large. But I wanted to see how this tube preformed with it’s low power tube plate resistance. Here is the distortion plot for the lower frequencies at 1W RMS mid-band power.
This is truly excellent low frequency performance and the 20Hz distortion number is less than half of what it is typically seen with SE-UL stages. Remember that these Edcor GXSE transformers are only rated to 40Hz. But these transformers clearly punch above their weight class.
These test results clearly show very capable amplifier. It has an output power rating just where I wanted it, it has good distortion characteristics, excellent bandwidth characteristics, and plenty of low end support. This is all great, but how does it sound?
Impressions
This amp sounds incredible! It has all the classic SET tonal characteristics but is also very fast and agile. And it delivers the low end with a power and presence that is exceptional. I mean “raises goose bumps” kind of exceptional.
As I said above, I threw just about every kind of music at this amp you could imagine. It never showed any signs of strain, distortion, or muddled sound at all. It was always clear and fast with that famous SET warmth and color.
I used Michala Petri’s recorder performance of “Frederick The Great : Sonata in B-Flat – Allegro” to test the amp’s speed and agility. It never missed a single beat of the very fast score and it was always as crisp and sharp as it is in person. To really test the low end I used Bachman-Turner Overdrive’s “Not Fragile – Quad Mix” off The Anthology album. This starts off with a strong bass riff that does not disappoint. Even over the other rhythm lines this strong bass comes through with great power and presence. I also used Norah Jones’s “Cold Cold Heart” off the “Come away with Me” album to see how the bass came through. This is another song with a strong ever present bass line. It never got lost or even a little muddy. It always came through smooth, crisp, and defined.
This amp makes me feel like I’m in the room with the musicians. The sound stage is wide and deep with excellent clarity.
Summary
This amplifier is an unqualified success. It was well worth the 19 month journey from initial idea to finished product. I strongly suggest, if you’re thinking about building a SET, you give this one a try. You won’t be disappointed.
So let me know what you think of the “The 6AS7 Purpleheart SET” amplifier.
A Note Concerning 6AS7/6080 Power Tubes
Previously, in the post “About That Bias Point”, I commented about the variability of the power tubes used in this amp. I currently have on hand 7 power tubes I can use in this amplifier; 2 of the 6080 variety, 4 of the 6AS7G variety, and one 6AS7GA. All of these tubes test as “good” based on emissions levels. All also seem to be fairly well matched between triodes; within about 10%.
Here’s how they work in the amp. One JAN 6080WC works really well. The other JAN 6080WC produces excessive distortion in one channel. One RCA 6AS7G causes low frequency oscillation in the left channel (I scrapped that tube). Of the two beautiful Raytheon branded 6AS7Gs (shown in this post), one is arguably the best tube in the amp, the other is a little low in one channel; enough to notice. The GE 6AS7G sounds pretty good and the GE 6AS7GA sounds incredible.
The lesson here is that this amp really is a marriage between good design and the right power tube. My recommendation for anyone building this amp is to lay in a bunch of power tubes, at least four or five, and audition them in the amp. The ones that work well, keep. Sell the others or use them in regulated power supplies.
This type of selection is the price we pay for using some tubes not specifically designed for audio in an audio amplifier. There is nothing wrong with this process. In the electronics industry, this process is called “select at test” and it’s rather common for “one off” and small unit number production. All I ask is that you don’t get frustrated if the first tube you try in this amp doesn’t meet your expectations. Try another. And when you find that right tube, you’ll be amazed at how it sounds.
Many amp designs I’ve seen use 100k log pots for volume control. You use 250k on every design I’ve seen. Would you elaborate on that?
Also, would the drive circuit you use here be appropriate for a 6B4G output stage with 45v on the Cathode?
Thank you for publishing all this wonderful information.
Volume controll choice is driven by two factors. First, is output impedance of whatever is driving the amp. The higher the value of the volume control resistance at the front end, the easier it will be to drive the amplifier. Second is the high frequency response of the volume control / driver tube combination. In this case, the value of the miller capacitance comes into play. If too large, it can affect high frequency response. This phenomenon is best described in this post: Volume Controls and High Frequency Response
As for the 6BG4 biased at -45V, this driver design would be overkill. In all probability the cascaded gain would be far too large. I’d stick with something like a single 12AT7/12AZ7 triode or maybe a 6SL7 as used on the 6L6 Spalted Alder amplifier.
Finally, an example of Miller capacitance that I can understand! My current daily listening amp is 6B4G with a 6SL7 driver stage, similar to.your 6L6 design. But I think the 250k pot is still in there from when it started life as a Lakewood. Next time I pop the hood I’ll consider some updates.
Hi Matt,
Another general theory question for you, this time concerning the power supply.
I ran a simulation and came up with the following for your PS design:
Power B+:
VRMS = 267 V
Difference between max and min at steady-state is 8.1 mV.
https://flic.kr/p/2oZzUJP
Signal B+:
VRMS = 306 V
Difference between max and min at steady-state is 2.1 mV.
https://flic.kr/p/2oZyRwL
Do you have design criteria when it comes to ripple voltage for the signal and power stages? Is there are reason you opted to put chokes in the power branches (compared to say the Marblewood)?
Many thanks.
I can’t speak to your simulations as I never use them. But your numbers look far too large for the topology shown.
My design criteria for power supplies is two fold. First I like to maintain a ripple factor of -90dB or about 0.003%. The second criteria that I like to have at least 40dB of channel separation between signal stages and more between power stages. Meeting this requirement generally results in even lower ripple factors than the -90dB.
I did the calculations by hand and got a 0.455 mV ripple for power B+ and 2.2 mV ripple for signal B+. So it seems I may have set up something wrong in the pwr stage simulation. Always good to do calcs by hand if possible (sanity check).
Thanks for sharing the design criteria you use.
Chiming in again to ask about the circuit. I’ve been setting up a spreadsheet to make AC coupling design easier to understand.
With your quiescent points, for the 12AU7, I’m determining a voltage gain of approx. 10 for stage 1 (cathode bypassed), and then a voltage gain of approx. 6.5 for stage 2 (unbypassed), and for the 6AS7, a gain of approx 1.5. Would this be a total voltage gain of 97.5?
For example, if I were to assume V_in = 0.5 V RMS, would this lead to V_out = 49 V RMS on the primary of the output transformer?
For your drive conditions table, where are you measuring V_out?
Many thanks Matt.
When I measure amp performance it is always measured at the input and output of the amplifier. So in the table with the three conditions, Vi is at the RCA jack input, and Vo is at the speaker terminals with an 8Ω dummy load.
There are times to worry about voltage gain and times to ignore it. In the case of the driver stages, your numbers are fairly close to my calculated values. And by knowing the gain of the signal stages you can calculate amp sensitivity and any feedback parameter if you so desire (I usually don’t). But in the power stage, voltage gain has little meaningful value. The real critical measure of power stage performance is power sensitivity. This is a measure of load power out in watts divided by the driving voltage at the input to the power stage. Since the power stage is usually the first step in amplifier design, the power sensitivity of the output stage informs the driver design. The end to end voltage gain will always look low because the output transformer represents a significant loss in voltage gain. But the end to end voltage gain of an entire audio power amplifier also has little meaningful value. You really want to know the power sensitivity of the whole chain, which is really what those tables show. They show how much voltage at the input is required for how much power in the load.
The cascaded 12AU7 driver was first designed for the 6336 SET amplifier. I then repurposed the design for the 6AS7 amp. Both power tubes are large triodes witch all typically share the characteristic of low power sensitivity. Hence they require a large voltage swing to generate significant power in the load. The entire development of tetrodes and pentodes was specifically to overcome this shortfall of power triodes.
I hope this clears things up.
Thank you. I just picked up a clean copy of Theory and Application of Electron Tubes (1944) for a whole $7. There is a great section on power sensitivity in there.
$7! That was a GREAT deal.
Matt,
A couple construction questions:
1. Regarding the speaker binding posts: I assume the bare post is not supposed to come into contact with the rear plate (which will be grounded). I sized the binder post holes according to the recommended size on the keystone data sheet, and I think they’re probably too small as there is always continuity between the posts and the plate (see image below). Is there a solution that you would recommend that does not involve cutting metal?
https://www.flickr.com/gp/163354486@N03/945D3LzQ38
2. What is the value of that metal film resistor across the indicator light (near the 6.3V output from the power transformer)? Is there an advantage to using a single resistor in this configuration or is it equivalent to the dual 100 ohm balancing typically used?
Here is a photo of my layout progress. Still waiting on the transformers, but wanted to ensure everything will line up. I’m using your layout as a general guide (as you can tell). I’ve had to make a few adjustments, but I’m pretty excited about it. (Sorry for the low quality images and photography).
https://flic.kr/p/2oXBGJy
Thanks,
Alex
Alex;
I see the problem. The holes for the speaker binding posts are far too small. If you take the other set apart and look at the part if the plastic base that goes against the metal, you should see circular ridges. These are meant to go into holes and center the binding posts. For the connectors I use (which look a lot like yours) my holes are 1/2″ in diameter, centered exactly 3/4″ apart. Those holes are not even big enough to use something like power transistor mounting isolators. I don’t see how you are going to get around making the holes significantly bigger.
The resistor to which you are referring is a 25Ω, 3W resistor that actually goes in series with the power indicator. This is to tame the brightness of the #44 indicator lamp. It’s something I like to do but is really not required. The heater center tap in this design is actually the white wire with the brown stripe connecting to the ground buss int he center of the picture.
Hope this helps.
Thanks Matt, yes this makes sense.
Is it the same situation with the RCA jacks? One of the plastic rings has a ridge that looks like it’s for the same purpose.
Yes that’s correct.
Here is a picture of the speaker holes in the back plate of the 6L6 Spalted Alder amp.
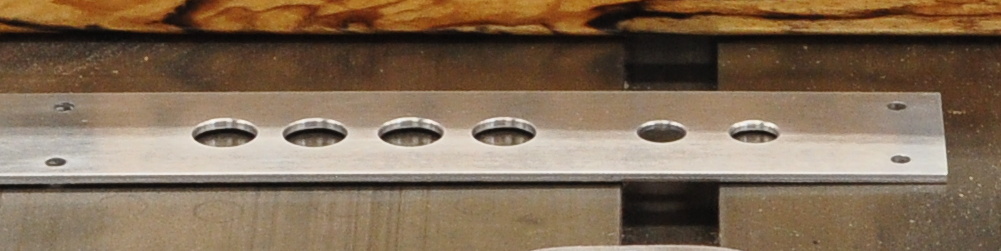
The holes on the right are the two 3/8″ holes for the insulated RCA jacks. The four holes on the left are for the speaker dual binding posts. These holes are 1/2″ in diameter.
Hi Matt,
I think I’m gonna give this amp a go. A couple questions:
1. I’m used to seeing Rd closer to the power transformer output (in your designs). Pardon my ignorance in circuit analysis, I’m an M.E. My interpretation of this is that you needed an additional voltage drop for the power stage and because you don’t have any resistors in the power branches, it made more sense to send the higher voltage to the signal stages (use the 1k’s to get them to proper B+), and then use Rd to get the correct plate voltage on the 6AS7. Am I anywhere near correct?
2. I’ve been doing my best at calculating voltage and power for some of the components. Can you tell me if the following ratings will work:
Power Section:
33 uF / 450 VDC (Qty. 3)
100 uF / 450 VDC (Qty. 3)
200 ohm / 10 W (Qty. 1)
1k ohm / 1 W (Qty. 2)
Amp Section:
0.068 uF / 400 VDC – Film (Qty. 2)
0.1 uF / 400 VDC – Film (Qty. 2)
47 uF / 25 VDC (Qty. 2)
68 uF / 200 VDC (Qty. 2)
100k ohm / 0.5 W (Qty. 4)
5.11k ohm / 0.5 W (Qty. 4)
2k ohm / 0.5 W (Qty. 4)
470k ohm / 0.5 W (Qty. 4)
1.2k ohm / 10 W (Qty. 2)
Many thanks!
You are correct concerning the power supply. The cascaded signal stages really need about 300V B+ to get the performance I wanted. But the power stage design point called for a 270V B+. This facilitated putting the dropping resistor after the first filter and the signal stage power pickoff. As a note, the 1kΩ resistor in the signal stage supplies only drop about 3V. But in combination with the 33µf capacitors yield 28dB of ripple reduction at 120 Hz (i.e. 2 x mains-frequency). Final B+ voltages in my build were 306V for the signal stages and 267V for the power stages.
Your part ratings look fine except for the 1kΩ resistors in the power section. Half watt ratings on these are fine as they actually only dissipate about 10mW (3.16e-3A * 3.16e-3A * 1000Ω ≈ 0.01W). 🙂
Hi Matt,
I’ve only just now discovered your blog. I have absolutely now experience building amps. However, I love SET amps, currently using a 84 and a type 45 amp. They’re both fairly low powered 1.5 – 2pwc. My speakers are 100dB.
I’ve toyed with the idea of a 300B amp, however I’d love to try something else, tried out my friend’s KT88 SE amp (8wpc). I’ve seen a 6BC5A SET and now yours. I wonder if you could comment on the comparison in sound between the 6336 and this 6AS7 amp. The 6336 seems to have a bit more power, but both should work with my speakers. Our music preferences seem to be very similar.
I have a friend here in New Zealand who builds amps and he’d be able to follow your designs and build.
He normally uses Hashimoto transformers which we can easily get. But Lundahl is also an option for us.
Best wishes and thanks for sharing your projects.
Holger.
Glad you are enjoying the site.
I will say, up front, of the two big SETs here I prefer the 6AS7 Purple Heart SET hands down. Not only is it a simpler build than the 6336 SET, but I think it sounds a little bit better in the higher registers. The difference in peak clean output power is only ≈4.6dB. With your speaker sensitivity of 100dB/watt this should make virtually no difference.
I do recommend you read the note at the end of the 6AS7 “Purpleheart” project page titled “A Note Concerning 6AS7/6080 Power Tubes”. These big triodes, both the 6AS7/6080 and the 6336, are not traditional audio tubes. As such, some tube rolling is required to get the most out of these amplifiers.
I hope this helps.
Thanks, Matt,
Can you recommend a replacement power trans as Edcor doesn’t make the one you use in 220V.
Also, have you tried 6SN7 tubes instead of the 12u7s?
Cheers,
Holger.
I would recommend the XPWR009 from Edcor. It’s technically a 225V primary but it should work fine. The specs are 550v(275-0-275)@175mA CT, 6.3V@4A, and 5V@3A.
I do have a cascaded design for the 6SN7 but it’s a slightly different beast. And the one drawback is that the first stage must be cathode bypassed to preserve the high end frequency response. This is due to the much larger Miller capacitance of the 6SN7 in the second stage. With this bypass, the end to end gain of the chain is ≈42dB or 126v/v. This means that for full drive the amp only requires about 480mV rms to get to full power. This makes the overall amp crazy sensitive.
Short answer is the replacement of the 12AU7s with 6SN7s could be done. However I think a little more Engineering would be in order.
Hi Matt,Quick question on the tranny, would the XPWR 219 550v 150ma ct, 6.3v 4 amp ct, 5v 3amp ct work just fine. I figured 2.5a + .6a =3.1 for the 6v tap. then using the 5v ct out. didn’t want to miss anything, better to ask an expert.
The short answer is yes, the XPWR219 will work fine for this amp. I would use the center tap on the 5V winding for the B+ instead of using the pin 8 connection on the rectifier socket. This is the approach taken on the 6L6 Spalted Alder amp. I have an in depth look at it in this post “6L6 SE-UL Transformer Wiring” showing how it’s generally wired..
Thank you for the reply Matt, if I could get a dimensional diagram I would be set to go. The 6v6 turned out to be the quietest amp I’ve ever built, thanks for everything u do.
Here is the top plate drill template I used.
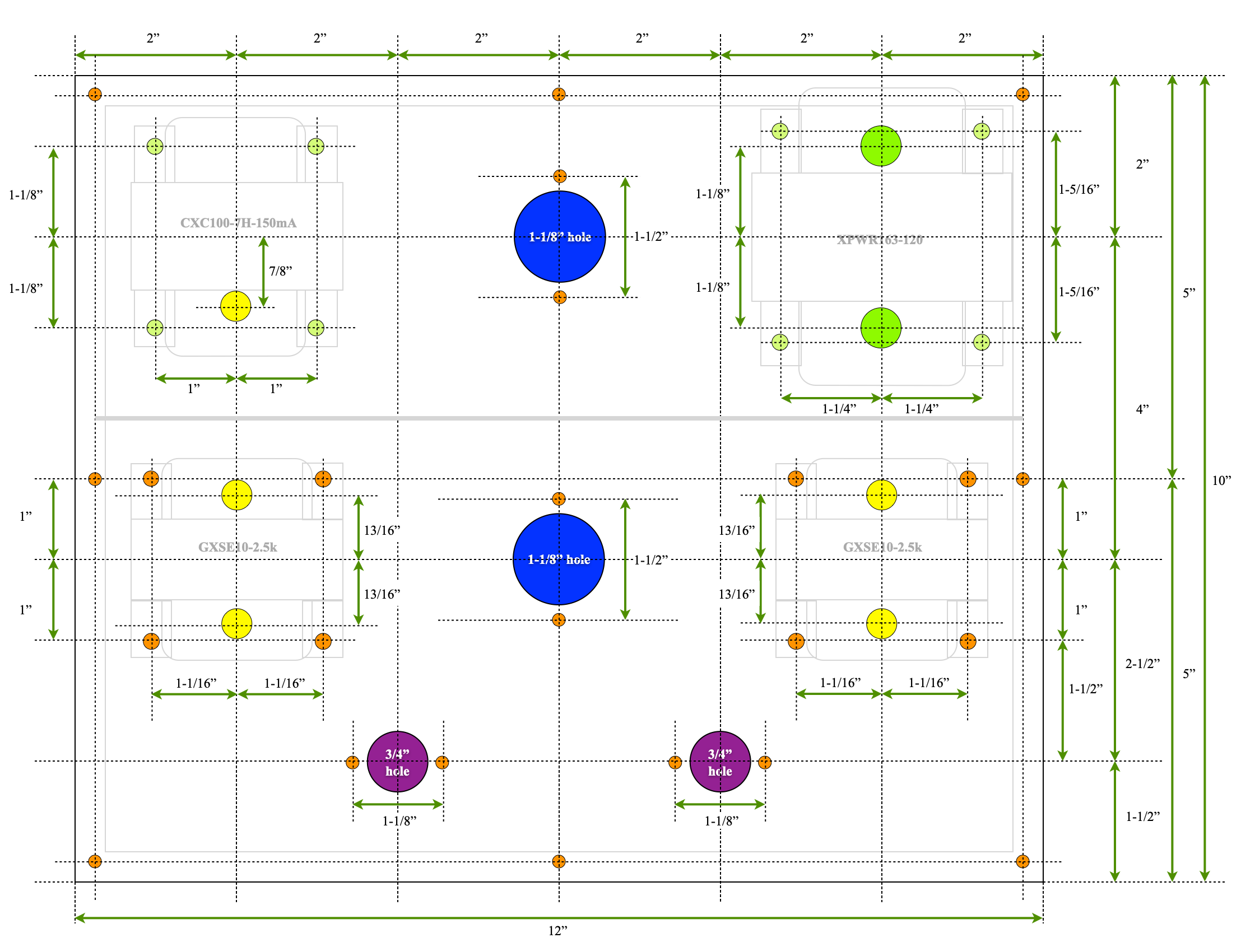
File Link: https://www.cascadetubes.com/wp/wp-content/uploads/2023/05/6AS7-SET-Top-Plate-Drill-Template.png
Be careful if you use a different power transformer. I recommend you get it in hand and carefully check the dimensions before drilling. I find that my templates seldom match the recommend drilling template supplied on the Edcor drawings.
Thanks Matt, I appreciate it I’ll double check everything. Thanks again.
Hi Matt
I am robert from italy
I have a question for you
Do you think it would be interesting to build a 6336 push pull amplifier?Or pp 6as7?
Sorry for my english….
Regards
Given what I now have learned about the matching of these big pass tubes, I would not necessary recommend a push-pull design. If I did, it would only be for the 6AS7 and I would strongly recommend that you stick to the modern production Svetlana tubes. I would also incorporate a large amount of balance margin in the design so that the power stages could be properly balanced.
Such an amplifier would qualify as a fairly advanced design due to the need to deal with part variability. In my opinion, it is really not warranted for the marginally increased power it would provide.
Such an amazing build and design. Well done.
Construction question that has been plaguing me: How do you make the cutout for the IEC AC plug in your chassis? It seems to be the age old question on every forum for makers. The only answer is “Dremel.” I really want a chassis punch but Greenlee is pricey and the closest rectangle isn’t really that close. Maybe you CNC? Also, an expensive answer to the problem. Thanks.
Glad you like the project. It’s the default amp in my office right now and I love the way it sounds.
The answer for the IEC plug is easy… but old school. I drill out the center and use a file to finish the opening. This is the layout for the power inlet side of the back plate.
This corresponds to the inserts I use. Yours may be different. The blue circles are 1/4″ holes drilled at the corners. Then I cut or drill out in between them and use some files to bring the final hole to shape, test fitting repeatedly as I go.
This may sound like a tedious process but in reality it only takes about 15 minutes total. There are lots of other options but this one seems to work best for me.
Facebook post makes reference to a 6877 tube and it being one half a 6080 in a 9 pin arrangement https://www.facebook.com/groups/310025952979348/permalink/1163482207633714/?mibextid=W9rl1R. If correct and common/inexpensive, this might be an interesting alternative to a single 6AS7. I am using a 6080 in the Grevillia spp. version of the Purpleheart—or was until the power transformer gave up the ghost.
Whereas I would never refer to the 6877 as “1/2 a 6AS7” it is an interesting tube. Compared to the 6AS7 (6080) it is lower power, with a higher µ and Rp. Ratings for max current, max plate voltage, maximum power dissipation are all significantly below the 6AS7. It is intended as a pass regulator in small power supplies especially in airborne equipment.
A quick web search does not show much information and virtually no availability. I only found data sheets from Bendix and Tung-Sol. It is rather likely that there were not very many made, making them interesting, but not a good candidate for new designs.
I have been enjoying this amplifier so much I find many excuses for not wanting to switch on the 300b. Unfortunately my 370 fx power transformer blew a 2A slow blow fuse and another. Long story short after a few emails and tests looks like there is something wrong with the primary winding and Hammond will send a new one. Pleased about their good customer interaction. So it’s back to the 300b for the time being. It still sounds almost as good after 3 years.
My experience has been that sometimes the heat of the Hammond power transformers, especially when run near maximum, can lead to early failures. However, Hammond has always been great about making things right. Now I just specify a larger capacity transformer if using a Hammond. The extra margin seems to make a lot of difference in long term performance and endurance.
Yes I had read the Hammond can run hot but this one after an hour of operation was only reasonably warm to the touch. The top plate of the amp does gets quite hot though.
Matt, my replacement 370FX arrived nicely timed for Christmas repairs. Noting your previous comment about “margin” is there any thing I can do to create a little more margin within the circuit?
My first thought for increased margin would have been to step up to the 370HX transformer. However, since you already have the FX in hand that’s mute. The other way to increase PS margin is to reduce the bias current on the 6AS7 triodes. This will decrease overall output power but will buy you some margin. Personally, I would just stick with the transformer and design you have. My guess is that you received a bad transformer the first time. I assume that the replacement will be better.
The replacement power transformer is in place. I decided to use the centre-tap for the power this time following your post on this in the 6L6 Spalted Alder thread, so needed to move a few things around. I measured plate and cathode voltages which haven’t moved too much if I recall correctly ie 253-254v and 81-82v for the 6080 plate and cathode, left/right. The 12au7 for the left channel is consistent at 160v for both plates and 8.4v for both cathodes. The right channel is close with plate voltage varying 1 or 2v and cathode no. 1 two tenths low. Just enjoying David Bowie Station to Station and the amp is demonstrating just how dynamic and “quick” it is. Crossed fingers the transformer holds out this time.
Glad to hear she back up and running.
Matt,
A few questions:
1. What brands of capacitors did you use for coupling and bypass? Do you have any preferences?
2. How important are the values of the film capacitors? I don’t have 0.068 uF film capacitor. So I put in a 0.022 uF I have. Can I replace both of the coupling caps with 0.1 uF and 0.18 uF? Will they be too large to hurt the performance?
3. I can source 4H 200 mA chokes cheaply. Can I replace the 2H 100 mA chokes with them? The 4H choke has a resistance of 68 ohm. Is it Too low?
I’ll answer your questions in order.
1) In the 0.1µf position between the second triode and the grid of the 6AS7 I used Cornell Dubilier 716 series polypropylene film capacitors P/N CDE716P400 104J. These are my preferred coupling capacitors in most amps. For the coupling between the two driver stages, I used a Panasonic ECW-F6683JL 0.068µf 600V metallized polypropylene film capacitors as I didn’t have any 716 or 715 series in this value.
2) The 0.022µf capacitor is too small for either position. I suggest that you use 0.1µf in both positions (i.e. all four coupling capacitors). This value will work acceptably well in both positions.
3) Replacing the 2H chokes with the 4H/200mA chokes will work without issues. The resistance is acceptable in this application.
I hope this helps.
Thanks for the reply. How about the electrolytic capacitors for cathode bypass and the 100 uF and 33 uF in the power supply? I used some salvaged capacitors I collected in the past and would like to try some newer or better ones.
Do you prefer to bypass the 33uF and 100uF with a film capacitor?
For these I just use good quality aluminum electrolytic capacitors. Usually either from Illinois Capacitor or Vishay/Sprague. I know some people like to use speciality capacitors for cathode bypass but I don’t think it’s necessary.
Appreciate your feedback.
I built an amp based on your design. My PSU is a SS voltage doubler with liberal amount of capacitors that I already have. As I only have a small 1.5H choke available, I used only resistors for each plate supply. The amp is absolutely quiet. I measured 0.3 MV noise at the speaker output.
Do you think a tube rectifier will sound better than SS for this amp design? If so, I may build one later.
You added one choke for each plate supply. It seems that the purpose is to further reduce AC noise. With my current dropping resistors at the plate supply, AC noise is 7 mV at the plate. I also cannot hear any hum. Should I replace some of the resistance with a choke? Will the amp gain anything more (e.g. transparency or dynamics) by doing so? If not, why did you add the chokes instead of resistors?
I’m glad your amp turned out well. As to the rectifier choice (tube verses solid state) it has been my experience that it is very difficult to tell the difference if the power supply is properly designed. My advice is if you like it, don’t change it. The power supply is obviously very quiet.
The insertion of the two chokes in the power stage B+ filters is much more about channel separation than overall noise reduction. They provide a good amount of B+ filtering but more importantly combined they provide over 80dB of channel separation between the left and right power stages. The PSRR and RC filtering is sufficient for the gain stages, but the power stages really need more active separation. These two chokes provide great channel separation even at near overdrive conditions. That is the primary reason they are there.
I hope this explains the topology more fully.
Really appreciate your reply!
Siting here in my office as the sky turns dark and the light fades, with some soft jazz playing in the background through the new amp, it strikes me that there are few tubes with as good an old amp glow like the 6AS7G in the big ST16 shouldered glass envelope.
I am happier with this amp every day.
Complete “the look”. Plug an old school 5U4G into the rectifier socket if possible.
Quick question on the VU meter box.
Since there is a switch and pilot light, can we presume that there is some active electronics inside?
Yes. There is a buffer and control board inside. I guess I’ll have to do a page for the meter box as well.
I would also enjoy learning more about the meters component. I have a few of those meters in my stash, but I’ve never used them. I’m not sure how.
The amp looks incredible. It’s true that one needs to personally experience a SET to understand how they sound. I never made one with sufficient oomph to be practical in my home. If I ever get all the other projects in my queue out of the way, this amp is the likely candidate — as opposed to the 6B4G design I have in my notebook. The “Purpleheart SET” would run cooler, which I like, not to mention the lower cost of 6as7 tubes…:-). I wonder how hot the 6as7 gets.
The 6AS7 has a 15.75W filament and the plates are running about 12.2W each. This brings the total heat dissipation in the tube to about 40W. So it gets warm but it’s not a burn hazard like the 6336 SET. I put a 5U4GB in the rectifier slot yesterday to see how the amp does with a little lower B+, and even with the increased heat dissipation of the rectifier, the top of the amp is only warm (not too warm to hold a hand on). It really sounds good.
It looks fantastic Matt, but what is it sitting on? Two extra sets of inputs and a very pretty front with the ammeters. The doubledecker look is really eye catching.
Ah yes; the other component. That is actually a standalone, dual channel, VU indicator for the amp (or any amp).
When I cut the purpleheart for the SET chassis, I had a considerable amount of the plank left over. I had always wanted to try out the ubiquitous little VU meters, however I was still unwilling to integrate them into the amp itself. I felt the risk to the basic amplifier operation was too great. So I got the idea of “matching components”. I even used the patina finish copper on the power panel so it really did match the amp. The design is totally pass through so it has no impact on the amp whatsoever.
Maybe I’ll do a post or project page just for that “VU box” component as well.
Just looked at the enlarged photo. I hadn’t noticed they were VU meters. I think it’s a really great piece of equipment and I like the fact that it’s standalone. I think it would be a nice project and hope that you do a post or project page for it. Any chance of a quick schematic, I fancy having this piece of equipment in my set up. I’d like to build the amp as well, but will have to see how finances go over the next couple of months. With postage and import tax, Edcor transformers are so expensive for me. I can get Hammond power transformers here in Europe, but haven’t tried to get output transformers here yet. Last time I ordered from Edcore I stocked up on output transformers but I’m now down to my last pair of GXSE10-5K-8’s which unfortunately are unsuitable for this amp. Also enjoying your prolific blogging.